Automazione su misura per produzioni flessibili
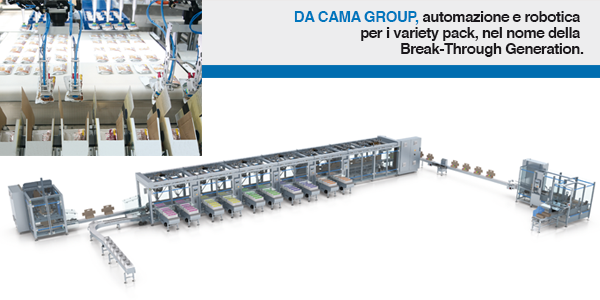
IMBALLAGGIO SECONDARIO: Cama propone sistemi ad alta ingegneria, versatili e adattabili a ogni produzione. Design e tecnologia, hardware e software per un confezionamento user-friendly, anche in versione multi-gusto.
Il “variety pack” (confezione multi-gusto) è diventato un must per il successo sugli scaffali dei supermercati: un più ampio assortimento di prodotti consente infatti di sfruttare al meglio lo spazio a disposizione e soddisfare le diverse preferenze dei consumatori. Ne deriva un’esigenza di flessibilità sia in termini di processo che di imballaggio, difficilmente conciliabile con l’elevato livello di standardizzazione richiesto fino ad oggi all’automazione.
Cama Group, fornitore di livello mondiale di sistemi di imballaggio automatico, deve gran parte del suo successo alla capacità di leggere le esigenze del mercato; inoltre, grazie ai forti investimenti in Ricerca e Sviluppo e alla cooperazione con Università e Istituzioni, risponde alla richiesta di flessibilità sempre più pressante espressa dagli utilizzatori finali, mettendo in campo sistemi all’avanguardia, ad alta efficienza e adattabili.
È il caso della Break-Through Generation, con cui l’azienda italiana ha introdotto un nuovo concetto di automazione per il packaging secondario, fornendo sistemi user friendly di alto contenuto tecnologico a tutti i clienti: garantisce cioè il giusto livello di automazione non solo ai grandi produttori che lavorano ad altissima velocità, ma anche a coloro che, pur realizzando un numero inferiore di prodotti/ora, cambiano spesso il formato del prodotto o la configurazione dell’imballo.
Robot e visione artificiale per linea di carico di un variety pack
IG270 è il nome in codice della nuova struttura modulare di Cama, che può variare il numero di unità robotiche a seconda delle esigenze produttive.
Ciò che colpisce di questo innovativo sistema pick & place è l’ingombro ridotto, possibile grazie al software anticollisione sviluppato dall’azienda di Garbagnate Monastero.
I robot di tipo Delta “made in Cama” condividono aree di lavoro comune, permettendo quindi di risparmiare spazio senza perdere efficienza e, soprattutto, evitando interferenze reciproche. In questo modo, l’isola robotizzata occupa il 40% di spazio in meno rispetto a quelle di concezione tradizionale, dove ogni robot lavora su una propria area esclusiva.
Grazie poi all’impiego di componentistica elettronica “on board”, non sono più necessari gli ingombranti armadi elettrici dove alloggiare azionamenti e componenti elettronici; inoltre, il ridotto utilizzo di cavi “taglia” i tempi di assemblaggio e, quindi, di start up della linea.
E le ricadute positive di questi accorgimenti sono immediate, a partire dai risparmi energetici che derivano dal fatto, per esempio, di non dover installare un sistema di condizionamento per evitare il surriscaldamento dell’armadio elettrico.
Dettaglio di un robot guidato da visione artificiale utilizzato su una linea per il confezionamento di doypack con tappo, caricati in configurazione multi-gusto. Le pouch, in arrivo su un nastro piano, vengono “viste” dal robot, che riconosce i diversi gusti e quindi sceglie quali prelevare per comporre il mix desiderato. |
Isola monoblocco: unità top loading flessibile e compatta
Spesso l’automazione a fine linea è un sogno per i produttori medio-piccoli che devono contenere i costi e non possono contare su grandi economie di scala, ma devono anzi fare fronte a continui cambi di formato (cosa che in genere “mette in crisi” la linea automatica, facendo lievitare i costi e limitando l’efficienza).
La risposta a queste criticità è il monoblocco IF316 (foto 2, a sinistra), anch’esso espressione della Cama Break-Through Generation, che combina formatrice, robot Delta per il carico dei prodotti e una unità robotica per la chiusura delle scatole in soli 2x3 metri. L’impianto gestisce fino a 500 prodotti/min (forma e carica fino a 30 scatole/min), garantendo una notevole flessibilità in termini di configurazioni di imballo. Il sistema gestisce i prodotti in arrivo sia di costa che in piano, caricandoli, a seconda delle esigenze, in scatole display dal forte impatto visivo, oppure in scatole di cartone ondulato per il trasporto.
Compattezza, efficienza ed ergonomia sono parole chiave per IF316, la più piccola soluzione integrata per l’imballaggio secondario disponibile sul mercato, senza compromessi tra flessibilità e velocità.