Macchine per imballaggi innovativi
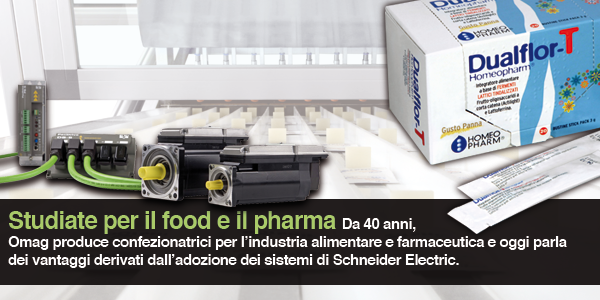
Kraft, Nestlè, Ferrero, Unilever, Bayer, Novartis sono solo alcuni dei clienti, che in oltre 100 paesi del mondo, utilizzano ogni giorno le macchine confezionatrici Omag.
Dal 1975, l’azienda di Gabicce Mare (PU) progetta e produce bustinatrici, dosatori e coclee per l’industria alimentare, farmaceutica, cosmetica e nutrizionale. Macchine confezionatrici studiate appositamente per risolvere “in automatico” le esigenze di un packaging innovativo. E oggi parla dei vantaggi derivati dall’adozione dei sistemi di Schneider Electric.
«La nostra produzione comprende una vasta gamma di confezionatrici verticali e confezionatrici orizzontali, a movimenti continui e intermittenti» spiega l’ingegner Giovanni Nocita, Direttore Vendite Omag. «Tra queste, la serie C3 per il confezionamento di prodotti in buste termosaldate su 4 lati, la serie CO per il confezionamento di prodotti in buste termosaldate su 3 e/o 4 lati in stile doy-pack o stand-up, la serie CS e Diva per il confezionamento di prodotti in stick pack, quindi le macchine per strip e pezzi singoli. A completare la gamma ci sono le “regine” di casa personalizzate per il settore farmaceutico e per questo catalogate come Pharmasachet e Pharmastick».
Ma sveliamo subito uno dei segreti di Omag: l’assenza di un vero e proprio catalogo di prodotti di serie. Ce ne spiega la ragione l’ingegner Roberto Filippucci, Automation & System Manager di Omag. «Pur essendo le nostre macchine progettate partendo da una base comune, individuabile nel loro principio di funzionamento, ogni macchina viene sempre realizzata tenendo conto delle specifiche esigenze di ogni cliente. In base alle sue richieste, sviluppiamo quindi una soluzione ad hoc, diversa dalle altre. Nel nostro ufficio tecnico, un team di progettisti opera a tempo pieno proprio per rispondere a queste necessità di customizzazione».
Packaging primario
In circa 40 anni di attività, Omag ha affrontato ogni tipo di problema relativo al packaging primario. «Siamo entrati in contatto con ogni tipo di prodotto, soprattutto in polvere, che deve essere imbustato e chiuso», spiega Davide Santi, Technical Manager Omag. «Dopo le prime esperienze in ambito alimentare, ci siamo orientati lentamente al settore nutrizionale parafarmaceutico, dove il nostro valore aggiunto ha fatto la differenza, soprattutto negli ultimi anni, quando cioè il mercato farmaceutico ha cominciato a richiedere macchine sempre più customizzate e in grado di confezionare più tipi di prodotto. Forti dell’esperienza sviluppata nel settore alimentare, caratterizzato da richieste estremamente variabili, siamo quindi entrati senza incertezze nel settore farmaceutico, perché la capacità di rispondere a richieste particolari era diventata il nostro pane quotidiano».
Omag si è avvicinata al farmaceutico con soluzioni innovative, tanto da depositare un brevetto importante relativo ai sistemi di dosaggio. Tale brevetto permette di dosare prodotti sia polverosi che scorrevoli, miscele comprese. Il successo riscosso nel mercato farmaceutico ha permesso a Omag di ottenere risultati positivi anche negli anni di crisi e di “riscoprire” il mercato italiano. «Se all’inizio curavamo poco il mercato domestico - afferma ancora Santi - negli ultimi anni abbiamo invece iniziato a seguirlo con maggiore attenzione, ottenendo grandi soddisfazioni. E abbiamo scoperto che, livello tecnico, quello italiano è un mercato molto stimolante: si ha a che fare con persone competenti, che parlano la nostra stessa lingua e che esprimono richieste di standard elevato». Per il mercato italiano, per esempio, sono state realizzate linee complete con l’utilizzo di robot.
«Proprio il mercato italiano ci ha spinto a utilizzare tecnologie molto avanzate - prosegue Santi - che, al contempo, hanno guidato una rivisitazione del “vestito” delle nostre macchine, non più degno del loro motore. Ne abbiamo quindi modificato il design, adottando gli standard dell’industria farmaceutica, rendendo le macchine più accessibili, più facili da sanificare, con meno cavi esterni, e così via».
Altro aspetto decisivo derivato dalla riprogettazione delle macchine Omag è la riduzione dei consumi energetici. «Siamo infatti riusciti a rendere più compatte le macchine, caratteristica apprezzata non solo dal mercato farmaceutico e - aggiunge Santi - grazie ai prodotti PacDrive Schneider Electric, ne abbiamo ottimizzato gli ingombri, soprattutto attraverso l’utilizzo dei motori con elettronica integrata».
Nel 2007 è avvenuto il matrimonio fra Omag ed Elau (successivamente acquisita dal Gruppo Schneider Electric). «Conoscevamo Elau già da qualche anno, ma non avevamo ancora le spalle abbastanza robuste per seguirne la filosofia, anche perché la preparazione di base dei nostri progettisti elettronici derivava dal mondo del PLC» riferisce il signor Santi. «L’ingresso in azienda dell’ingegner Filippucci (che ha preso il posto del padre dopo un’importante esperienza lavorativa in una multinazionale) è stato motore della svolta di Omag, anche perché ormai tutti avevamo le competenze necessarie per portare avanti il progetto. Da notare, però, che la nostra evoluzione non è mai avvenuta a scapito di scelte fatte in passato: ancora oggi siamo disposti a esaminare qualsiasi tipo di problema dei clienti e a mettere in discussione le nostre scelte. Questa filosofia è stata premiante e il tempo ci sta dando ragione».
Una partnership vincente
Perché Omag ha scelto i prodotti PacDrive? «Abbiamo analizzato i competitor presenti sul mercato e dei loro prodotti. All’epoca, oltre a Elau, oggi parte di Schneider Electric, c’era un solo fornitore che proponeva il motore con azionamento integrato» interviene l’ingegner Filippucci. «Questa soluzione ci piaceva, perché le nostre macchine avevano due quadri elettrici: uno dedicato agli azionamenti e uno dedicato alla parte di controllo. Due quadri, in termini di cablaggi e di spazi, cominciavano a essere impegnativi; ci siamo quindi indirizzati verso la tecnologia del motore con azionamento integrato, che avevo già potuto apprezzare. C’era poi il vantaggio, non indifferente, di poter utilizzare librerie software con molteplici funzionalità, che hanno semplificato la scrittura del software delle nostre macchine. Inoltre, l’ottimo rapporto sul piano commerciale e tecnico instaurato con il produttore non ci ha lasciato più alcun dubbio e abbiamo fatto la nostra scelta».
Con la soluzione PacDrive, Omag è partita dal cuore della macchina, ossia dal controllore e dal sistema di motion.
«Dopo l’integrazione di Elau nel gruppo Schneider Electric abbiamo iniziato a utilizzare molti altri prodotti dello stesso fornitore, che abbiamo potuto conoscere e integrare, a partire dagli inverter (ATV312). Oggi, in particolare, utilizziamo i sistemi di motion PacDriveM, ma stiamo già provando il sistema PacDrive3».
Afferma l’ingegner Lorenzo Degli Esposti, Sales Manager Schneider Electric: «Il sistema di motion control PacDrive può dare ottimi risultati. Con il nostro supporto tecnico e mesi di studio, programmazione e prove l’obiettivo è stato raggiunto. Omag ci ha concesso la massima fiducia, che ci impegniamo a mantenere in termini di aspettative di servizio e di evoluzione del prodotto. Perché il nostro prodotto deve evolvere insieme alle macchine Omag; e se un prodotto deve essere performante e affidabile, il servizio tecnico che sta dietro il prodotto stesso (progettazione, tempi di consegna, service e così via), soprattutto in ambito alimentare e farmaceutico, deve essere ad altissimo livello».
Degli Esposti prosegue sottolineando che introdurre su una macchina dei prodotti a capitolato richiede non solo un avvallo tecnico, ma anche un’analisi economica. Infatti, accanto al cuore della macchina, in cui sono determinanti una certa scelta e una certa soluzione di carattere prevalentemente tecnico, vi sono componenti dove anche l’aspetto economico gioca un ruolo importante. «Il nostro obiettivo è sempre quello di lavorare in partnership, quindi in armonia con il cliente, proponendo l’intera offerta Schneider Electric. Tuttavia, il vantaggio della scelta monofornitore deve sempre coniugarsi con il vantaggio del cliente a integrare dispositivi di qualità, al giusto prezzo e inseriti in modo armonizzato con i dispositivi preesistenti».
È stata importante anche la valutazione degli I/O TM5 successivamente collegabili su bus di comunicazione Sercos III che, in un’ottica di passaggio all’architettura PacDrive3, potrebbe permettere di integrare ulteriormente la ssoluzione di automazione sulle macchine Omag. «Quando si cambia una parte fondamentale della macchina (in questo caso, passando al sistema PacDrive3) è giusto guardare avanti per cercare di raccogliere le sfide e le occasioni del mercato - interviene Filippucci - e contemporaneamente, bisogna guardare avanti anche da un punto di vista tecnologico; la lungimiranza è sempre stata una caratteristica di Omag, che infatti sta già provando i motori con azionamento integrato ILM del sistema di Motion Control PacDrive3. Il passaggio dal sistema PacDriveM a PacDrive3 è possibile solo perchè vengono assicurate la stessa affidabilità e lo stesso software collaudato anche sulla nuova tecnologia, che offre notevoli plus come la comunicazione su Sercos III».
Automazione integrata e risparmio energetico
«La decisione di introdurre la tecnologia PacDrive sulle nostre macchine - afferma l’ingegner Nocita - ha incontrato all’inizio qualche difficoltà, relativa al fatto che gli end user chiedevano di avere l’automazione macchina gestita solo dal PLC. Il fatto di non avere più un PLC ma un prodotto che “fa qualcosa in più e di diverso” può generare qualche resistenza, superata dal fatto che poi viene apprezzato, in virtù del valore aggiunto che i dispositivi di ultima generazione portano alle macchine a elevato contenuto tecnologico. Oggi piace molto il concetto dell’azionamento integrato nel motore brushless, così come la possibilità di cambiare il servomotore con un semplice plug, per non parlare della riduzione dei componenti a magazzino, con un solo tipo di motore che viene programmato direttamente sulla macchina».
«Spesso, il valore e i plus di questa nuova tecnologia non sono percepiti in fase preliminare, finché non vengono toccati con mano» concorda l’ingegner Filippucci. «I primi vantaggi che normalmente vengono apprezzati dal cliente sono quelli più visibili, ovvero la riduzione dell’ingombro e il design più pulito della macchina. Un altro aspetto importante è il risparmio energetico, a cui si aggiunge la possibilità di diagnosi e assistenza remota. Per quanto riguarda il risparmio energetico, esso viene attuato innanzitutto a livello di hardware della macchina, ad esempio collegando tutti i motori sullo stesso bus in modo da permettere lo scambio energetico fra i motori stessi e permettere lo stoccaggio di energia nell’alimentatore. Vi è poi una fase di pianificazione e ottimizzazione del moto della macchina tramite il software di gestione del profilo di moto, cercando di implementare i profili più raccordati possibili, compatibilmente con il funzionamento della macchina. Mediamente, facendo una stima su 8 ore di funzionamento, abbiamo valutato un risparmio energetico del 20% circa.
Potendo raccordare i movimenti in modo armonico e con curve non limitate al profilo trapezoidale (tipico dei motori asincroni) si è ottenuta una gestione della meccanica e del motore elettrico che hanno prodotto un saving energetico, una minor usura degli organi in movimento e un minore stress meccanico della macchina. In questo modo, i periodi di manutenzione si allungano, si possono dimensionare in modo più corretto organi meccanici in precedenza spesso sovradimensionati per assorbire le vibrazioni indotte dal motore. Ne giova, in ultima analisi, la durata della macchina».
«Per Schneider, d’altronde, il tema del risparmio energetico è molto importante» afferma Degli Esposti. «Di fatto abbiamo una profonda esperienza nella gestione dell’energia, in tutte le forme possibili: dal fotovoltaico alle cabine, tematica molto avvertita dagli end user».
Nel settore del packaging, Schneider Electric mette a disposizione strumenti (come il software ECAM) e servizi specifici per stimare e ottimizzare già in fase di progettazione il consumo energetico della macchina. Questi risultati saranno confrontati con i dati di consumo reali registrati durante il funzionamento della macchina nelle varie fasi produttive per valutare la possibilità di un maggiore risparmio energetico.
«E quando troviamo delle realtà come Omag giovani, dinamiche, ricettive, volte al miglioramento costante riusciamo a proporre questi concetti» sottolinea Degli Esposti. Lo conferma l’ingegner Nocita: «Ci piace rischiare, se siamo convinti che una certa soluzione sia effettivamente quella ottimale. Con il sistema PacDrive e Schneider Electric riusciamo a trovare questa spinta e questa collaborazione per potere raggiungere anche nuovi mercati che altrimenti sarebbero inaccessibili».
Ancora vantaggi
Un altro vantaggio ottenuto con l’adozione della tecnologia PacDrive Schneider Electric, secondo Nocita deriva «dall’impiego di servomotori con azionamento integrato che permette di ridurre le dimensioni e gli ingombri perché consente di diminuire il numero di componenti a bordo macchina.
E ancora, legata a questa scelta, è la possibilità di standardizzare i motori della macchina; quindi il cliente ha solo due parti di ricambio diverse in magazzino il che si ripercuote anche sulla fase post-vendita, perché il cliente può ridurre notevolmente gli interventi di manutenzione, ma soprattutto il numero di parti di ricambio. Da quando ha iniziato a utilizzare questa tecnologia, Omag non ha più una richiesta così elevata di ricambi da acquistare, proprio perché di fatto la manutenzione è molto più efficiente, il numero di componenti è ridotto, la meccanica è stata in gran parte sostituita dall’elettronica (non ci sono più frizioni, catene e così via)».
«Ottimizzare le taglie dei motori ha previsto un notevole lavoro di progettazione» puntualizza Filippucci. «Riprendere un progetto meccanico per ridurre il numero di motori di tipo diverso è sinonimo di collaborazione tra l’ufficio elettronico e meccanico di Omag e il supporto tecnico PacDrive di Schneider Electric. Lo testimonia lo studio che viene fatto sulle macchine, che sono sempre più customizzate sulle esigenze del cliente. Ed è questo che crea il valore aggiunto, oltre all’affidabilità e alle prestazioni della macchina».
Esempi di oggi e programmi di domani
Pharmasachet e Pharmastick sono punti cardine dell’offerta di Omag, sia per le soluzioni tecnologiche adottate sia per il successo che riscuotono sul mercato.
Si tratta di macchine studiate per il comparto farmaceutico, destinate a produrre bustine saldate sui quattro lati o stick.
In particolare, la confezionatrice per stick, oggi molto richiesta dal mercato farmaceutico per confezionare polveri, è dotata di un dispositivo a coclea brevettato da Omag, che facilita il confezionamento di polveri di difficile scorrimento. «Parliamo di una macchina verticale a movimenti intermittenti, per bustine monodose stile stickpack» spiega Nocita. “Lo stickpack è partito da una richiesta importante nel mercato alimentare e oggi si affaccia sul mercato farmaceutico in misura crescente. Rispetto alla bustina saldata, lo stick permette di risparmiare intorno al 15-20% di materiale d’incarto a parità di dose da confezionare».
Il confezionamento dello stickpack richiede dispositivi molto precisi. Nel caso di un dosaggio a coclea, per esempio, la coclea, alimentata da un servomotore PacDrive iSH con azionamento integrato, deve essere lavorata a pieno con un’elevata precisione. Nello stesso tempo, il servomotore permette di gestire tutti i diversi parametri della coclea, in modo da dosare i prodotti con una tolleranza strettissima. Ciò è fondamentale soprattutto in campo farmaceutico, dove i prodotti sono molto costosi e la normativa è molto rigorosa.
«Nella gestione della polvere entrano spesso in gioco diversi processi di lavorazione, e non tutti i produttori hanno le risorse per garantire la giusta consistenza di scorrevolezza della formulazione» aggiunge l’ingegner Nocita. «Laddove non è possibile lavorare le polveri in un granulatore, esse arrivano quindi dalla miscelazione diretta degli ingredienti e la miscela risultante può essere poco scorrevole. In questo caso, è necessario utilizzare coclee altamente specializzate, così da garantire la precisione richiesta.
Il sistema brevettato Omag, che lavora sul principio della depressione, unitamente alla coclea gestita da servomotore PacDrive iSH, garantisce le elevate performance della macchina e anche la precisione di dosaggio indipendentemente dalla scorrevolezza del prodotto. La stessa macchina, con differenti qualità di prodotto primario, lavora garantendo sempre i risultati attesi con le performance di velocità previste».
La forza di questo brevetto Omag sta proprio nel riuscire a confezionare con la stessa macchina un’elevata varietà di prodotti polverosi con diversa scorrevolezza. All’intelligenza di Omag e delle persone che lo hanno sviluppato, il sistema PacDrive di Schneider Electric unisce la possibilità di movimentare il sistema con la precisione dei suoi servomotori, perché la coclea si muova esattamente di quanto previsto. «La precisione ha un prezzo in termini di costruzione del motore, di tipo di azionamento e di encoder» sottolinea Degli Esposti. «Con Omag è stata creata una partnership anche in relazione al posizionamento economico dei prodotti, perché i mercati richiedono elevate prestazioni a un prezzo in ribasso tendenziale». L’ingegner Nocita concorda: «Pharmasachet e Pharmastick, ma anche i nostri prodotti dedicati al mercato alimentare, si distinguono sia per la qualità che per il prezzo. E la loro competitività è stata indubbiamente favorita dalla partnership instaurata con Elau prima e con Schneider Electric dopo, dal momento che la soluzione PacDrive costituisce gran parte dell’elettronica utilizzata sulla macchina».
I programmi futuri - Omag ha già sviluppato il prototipo di una nuova macchina che verrà utilizzata per testare la nuova tecnologia di Motion Control PacDrive3 basata su bus di motion Sercos III. Questa tecnologia permette non solo maggiori prestazioni, ma anche una maggiore facilità di utilizzo per gli sviluppatori, grazie a un nuovo ambiente di sviluppo software SoMachineMotion. Il nuovo bus di comunicazione verrà utilizzato non solo per la trasmissione dei dati di motion, ma anche per l’acquisizione di segnali dal campo.
«Tutto il lavoro precedente ci ha permesso, nel 2011, di consolidare la nostra posizione di leadership nel mercato nutrizionale in Italia, in particolare nel segmento degli integratori alimentari energetici» conclude Nocita. «Possiamo infatti affermare che tutte le aziende che operano in questo mercato in Italia hanno macchine Omag. L’obiettivo è di ampliare questo dominio al resto del mondo. Oggi, oltre a mantenere la leadership nel mercato russo, dove siamo presenti dal 1985, stiamo dedicando tempo ed energie per operare in altri mercati come l’India, la Cina, il Brasile o gli Stati Uniti. Paesi, quindi, dove la concorrenza è elevata, ma i risultati raggiunti ci incoraggiano a proseguire. Nello stesso tempo, all’attuale stabilimento produttivo di circa 2000 mq ne stiamo aggiungendo a breve distanza un altro di circa 4000 mq, aumentando quindi la capacità produttiva e raddoppiando le forze che metteremo in campo per la conquista di questi nuovi mercati. Saranno disponibili anche nuovi uffici, un nuovo showroom e una nuova officina ad alto contenuto tecnologico, che ci permetterà di sviluppare al nostro interno ogni singolo pezzo delle macchine. Infatti, Omag riesce in maniera autonoma a costruire internamente ogni pezzo delle sue macchine, a esclusione di quelli commerciali. Questo è importante per potere garantire una risposta adeguata anche ai clienti che hanno bisogno di macchine o di semplici pezzi di ricambio in tempi rapidi».
Omag ha presentato l’intera gamma delle proprie macchine alla fiera Ipack-Ima (Milano, 28 febbraio - 3 marzo 2012), ottenendo ottimi riscontri.