Questione di resistenze
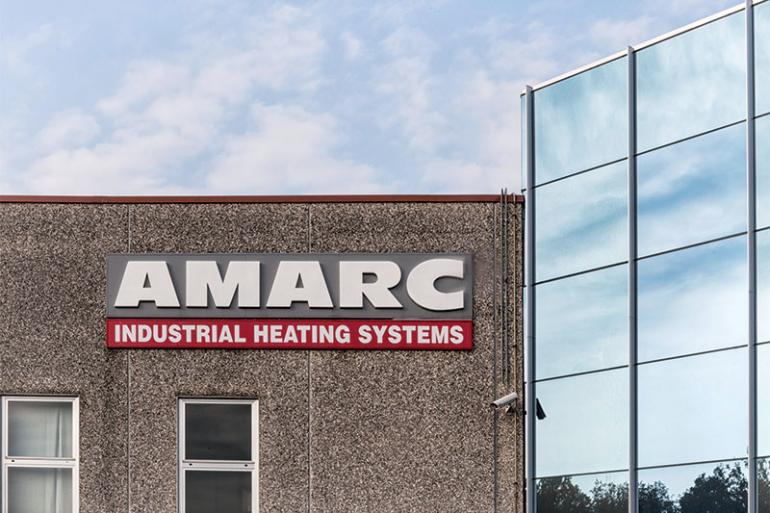
La differenza sta sempre nei dettagli. Nel caso in oggetto si tratta di resistenze in fusione di alluminio utilizzate sulle macchine per l’imballaggio, che garantiscono durata, affidabilità, efficienza e sicurezza superiori. Plus interessanti sia per i costruttori di macchine che per gli end-user. Questa soluzione “alternativa”, proposta da Amarc, può essere valutata al meglio magari dopo una prova “sul campo”, ovvero richiedendo all’azienda una campionatura gratuita.
E, allora... perché non provare? di Stefano Lavorini
Le resistenze in fusione di alluminio o di bronzo sono un componente della parte calda di formatrici - riempitrici - chiuditrici (HFFS e VFFS) e termoformatrici. Prodotte da Amarc rappresentano, a detta degli uomini dell’azienda di Montevecchia (LC), una scelta vantaggiosa rispetto alle tradizionali resistenze elettriche, utilizzate per la termoformatura e la chiusura di vaschette, nonché saldatura di film plastici.
Dati alla mano, le piastre con resistenze corazzate interfuse offrono un ottimo isolamento elettrico - anche in condizioni gravose - e temperatura uniforme su tutta la superficie, con in più il vantaggio di un singolo collegamento elettrico, a prescindere dalle dimensioni.
Permettono inoltre di ridurre in modo significativo i consumi elettrici (-30%) e, grazie alle elevate proprietà meccaniche e di resistenza alla corrosione, garantiscono una prolungata durata nel tempo rispetto ad altre tecnologie, con conseguente drastica riduzione degli interventi tecnici di manutenzione.
Tra l’altro, in Amarc, sono talmente convinti della validità del prodotto da offrire una garanzia di 3 anni sulla parte elettrica.
Un componente di valore
«Le resistenze in fusione prodotte da Amarc sono frutto di un’esperienza pluridecennale nella progettazione e realizzazione di prodotti e soluzioni per il riscaldamento e la trasformazione dei materiali nei processi industriali: in particolare, camere calde per il riscaldamento di fusti e cisterne, nonché forni industriali per molteplici applicazioni» mi racconta Giorgio Ardesi che, col cugino Andrea, gestisce l’azienda di famiglia fondata dal nonno.
«Tutti i nostri prodotti sono caratterizzati da un’elevata ingegnerizzazione e tecnologia e sono pensati per garantire semplicità di utilizzo, elevata efficienza termica, massima sicurezza funzionale.
Nel caso delle resistenze in fusione, in cui l’elemento riscaldante è “annegato” nel materiale, la principale caratteristica è che non c’è scambio termico con l’aria, il che assicura una maggiore durata nel tempo, ovvero una drastica riduzione dei fermi macchina - vuoi che si tratti di termoformatrici, tray seal o flowpack - nonché un significativo risparmio energetico.
Ma non è tutto. Un’unica resistenza, che scambia calore in sicurezza all’interno della fusione di alluminio, offre il vantaggio di avere un solo collegamento elettrico, semplificando così la manutenzione, nonché la garanzia di uniformità di temperatura nel tempo anche su piastre di grandi dimensioni».
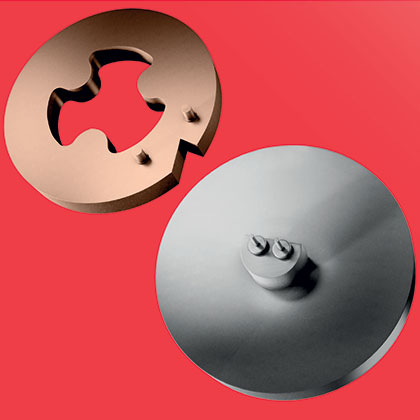
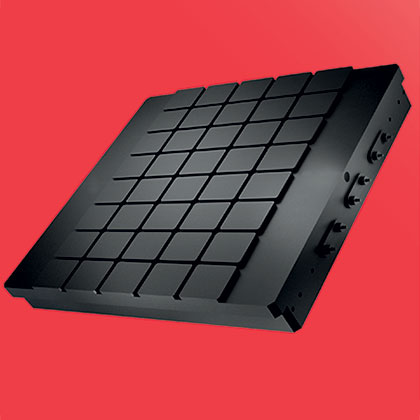
A ognuno la sua
Amarc realizza piastre riscaldanti in fusione su specifiche del cliente, sagomandole e lavorandole con macchine CNC; si tratta di piastre che possono raggiungere temperature di utilizzo di oltre 300 °C e possono essere predisposte per collegamenti elettrici in custodia con protezioni IP55 e IP65.
Nel caso, ad esempio, delle macchine HFFS (flow-pack) sono state sviluppate resistenze in fusione circolari per la saldatura trasversale del film di confezionamento.
Come ha modo di sottolineare il responsabile tecnico, Umberto Riboldi, «anche in questo caso mettiamo in campo la nostra disponibilità ed esperienza per definire, in collaborazione con il cliente, le caratteristiche più idonee del prodotto. Interveniamo, ad esempio, sulle caratteristiche della lega di alluminio, sulla tipologia della fusione, sui trattamenti superficiali per migliorare anti-aderenza e scorrevolezza o ridurre l’abrasione. Da decenni siamo partner di un’azienda leader a livello globale, con migliaia di installazioni nel mondo, e non abbiamo riscontrato problemi di tenuta delle saldature con qualsiasi tipologia di materiale plastico, compresi i nuovi polimeri biodegradabili o provenienti da fonti rinnovabili».
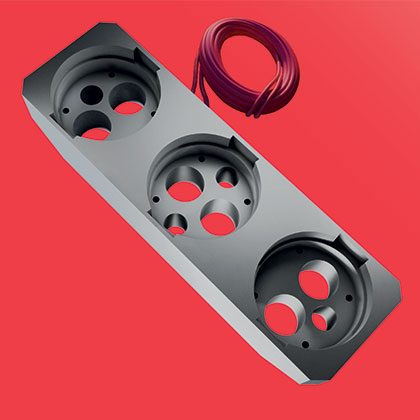
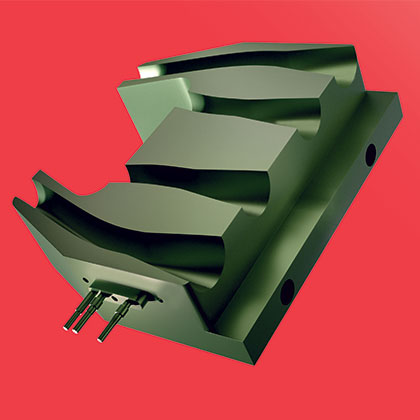
Dalle parole ai fatti
I sistemi saldanti, dunque, sono sì un componente, ma essenziale: se non funzionano a dovere, non si fa produzione. Per questa ragione Amarc si propone come un’azienda da sempre attenta al miglioramento di prodotto e di processo, con tanto di sistema di qualità certificato ISO 9001:2008.
Andrea Ardesi è chiaro al proposito: «Siamo un’azienda orientata al cliente, il che vuol dire, ad esempio, che non abbiamo un catalogo ma è il nostro ufficio tecnico ad affiancare il cliente nella scelta della soluzione più idonea alla singola applicazione.
Per quanto riguarda le piastre riscaldanti - continua - comprendiamo bene che i costruttori di macchine possano essere restii a sperimentare nuove soluzioni, e quindi, proprio per questa ragione, ci impegniamo a fornire, a chi lo richiede, un campione gratuito per fare un test e una prima valutazione.
Inoltre, la passione e la cura che mettiamo nel nostro lavoro ci permette di assicurare tempi di consegna delle piastre elettriche in fusione estremamente ridotti, anche di soli 3 giorni lavorativi, nonché una garanzia fino a 3 anni sulla parte elettrica».
Tirando le somme, sembra proprio che ci siano ragioni concrete per approfondire la conoscenza e mettere alla prova questa tecnologia alternativa, che pare proprio in grado di offrire ai costruttori di macchine e agli utilizzatori vantaggi concreti.
A voi la scelta.