Tecnologie abilitanti per la smart factory
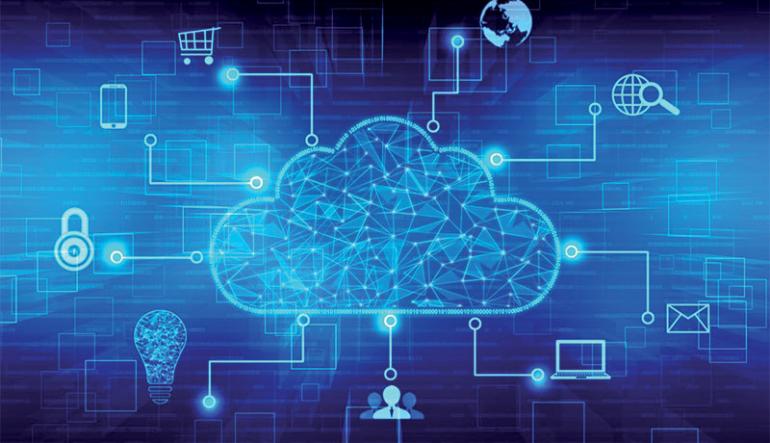
Molti sono i punti di forza delle tecnologie IOT, ma non è facile realizzare l’infrastruttura che sia in grado di “far fare un salto” al business. Il ruolo di Competence Center, fornitori, OEM, system integrator ed end user.
Maurizio Cacciamani
Molti sono i punti di forza delle tecnologie IOT: interazione bidirezionale con i sistemi di controllo, ambiente di sviluppo di dashboard sofisticate (mashup ovvero unione di elementi, dati e informazioni di natura eterogenea, per ottenere risultati più utili rispetto ai dati di partenza ), integrabilità dei sistemi business, connettività illimitata, ambiente di sviluppo di modelli di Machine Learning codeless, rilevamento in tempo reale delle anomalie, disponibilità di strumenti di analisi statistica avanzata, installazione su cloud od on-premise (cioè installate sul computer dell’utente o su un server aziendale).
Non è facile integrare le tecnologie abilitanti ed è inutile nasconderlo: gli OEM incontrano difficoltà in quanto se è vero che ci sono realizzazazioni di successo (come quello illustrato da Emanuele Quarin, Digital Industrial Operations Director EU Electrolux), è vero anche il contrario. Tutti gli appartenenti alla filiera, ciascuno nel proprio ruolo, devono abilitare i pezzi della smart factory che deve essere semplice da gestire con device multifunzione adattabili facilmente alle diverse esigenze.
Rivestono grandissima importanza:
- la connettività, in modo da disporre dei dati in tempo reale utilizzando anche smart phone, tablet e smart watch;
- il coinvolgimento delle persone, in modo che possano, come in Elettrolux, portare valore aggiunto contribuendo a risolvere i loro problemi pratici;
- la formazione a tutti i livelli (dai manager fino agli operatori), che andrebbe sviluppata ulteriormente dai vari piani governativi.
Cosa fa il Competence Center SMACT? «I Competence Center sono “una” soluzione, non “la” soluzione al trasferimento dell’innovazione alle PMI» sostiene Matteo Faggin, Direttore Generale SMACT Competence Center. Il trasferimento avviene attraverso visite guidate a linee pilota e installazioni di successo, corsi di aggiornamento / formazione a dirigenti e operatori. È in preparazione il catalogo corsi (anche con webinar on line) il cui programma non andrà a sovrapporsi a quanto fanno già Università, Master e aziende. Servizi importanti offerti sono la gestione dei processi di innovazione, i bandi di finanziamento (a settembre il secondo di 900 mila €). In futuro verranno implementati nuovi processi e nuove soluzioni.
Cambio prodotto rapido. «Si può fare con successo!» spiega Carlo Cuppini, Head of Global Account Managers - Southern Europe B&R Automazione Industriale «con i sistemi di trasporto intelligenti: la linea deve essere modulare, dotata di scambi e rami paralleli, ma soprattutto espandibile: il carrello deve essere indipendente per percorso, velocità e carico».
A livello di integrazione, il controllore del robot deve dialogare con quello della macchina o dell’impianto condividendone gli allarmi, gli stati, i comandi e il programma del robot. Un’integrazione ulteriore vedrà la scomparsa del controllore del robot in quello della macchina/impianto. B&R ha sviluppato il proprio sistema di visione proprio per ottimizzarne l’integrazione nei propri sistemi per gestire al meglio la tracciabilità e i lotti anche molto piccoli.
La natura risolve problemi complessi con semplici soluzioni. «Partendo da questa considerazione - afferma Alessandro Ferioli, Industry Segment Manager Festo Italia - la società ha lanciato da qualche anno il progetto Learning by Nature che sta alla base delle attività di ricerca su materiali, software, integrazione». Ferioli ha sottolineato che “pezzi” di ricerca vengano inseriti nei prodotti citando l’esempio del robot collaborativo, dove la fluidica si coniuga con le più recenti innovazioni in campo digitale. Ferioli ha rimarcato come sia fondamentale in questi tempi la formazione soprattutto dei manager, chiamati a gestire notevoli cambiamenti organizzativi aziendali.
L’evoluzione della safety. La disponibilità di controlli distribuiti permette con un unico software la programmazione di dispositivi situati in luoghi differenti anche molto lontani dal controllore.
«Safety e security sono due facce della stessa medaglia» spiega Giovanni Sangiorgio, Divisional Manager Systems Pilz Italia. «Occorre progettare fin dall’inizio le nuove macchine tenendo conto di queste due facce in modo da non dover mettere successivamente costose “pezze”». Pilz ha sviluppato internamente un robot collaborativo proprio per capire le problematiche safety e security implicate e per poter sviluppare soluzioni ad hoc.
Sicurezza & produttività. Secondo Paolo Zanetta, Product Marketing Manager Automation products Datalogic, oggi la sicurezza non è più in contrasto con l’efficienza produttiva. Per evitare la neutralizzazione dei sensori di sicurezza sono disponibili modelli difficili da neutralizzare o sensori intelligenti che prevengono la manomissione. L’evoluzione ha portato a sensori insensibili ai disturbi ambientali che potevano causare l’arresto della linea e a modelli optoelettronici in grado di monitorare la sicurezza in contemporanea su più zone diverse che variano dinamicamente. I laser scanner ora sono in grado di rilevare le misure degli oggetti che gravitano intorno al robot mobile, una volta inviati al controllore questo calcola la localizzazione e il percorso del veicolo.
Come mettere in sicurezza una control room. «Basta installare sui PC Windows, che costituiscono la stragrande maggioranza dell’hardware delle sale cotrollo, solo ed esclusivamente il software strettamente necessario al funzionamento della linea» così Andrea Scattina, Channel & Sales Manager Italy Stormshield, azienda del gruppo Airbus che opera nel settore della cybersecurity offrendo soluzioni scalabili in grado di soddisfare tutte le esigenze anche quelle delle PMI che sono i clienti più numerosi. Per coniugare prestazioni con la sicurezza l’azienda ha realizzato blocchi che sono in grado di evitare che la linea vada in errore a causa di un’intrusione.
Come evolve il PLC. Per Alessandro Favero Product Manager Control Systems & IO Phoenix Contact il PLC si sta evolvendo verso l’edge: per cui è programmabile con linguaggi di alto livello, invia dati sul cloud, è in grado di monitorare da remoto con segnalazione via mail dei problemi, può installare App disponibili da store, gestisce la sicurezza tramite accessi controllati o accessi VPN. Queste caratteristiche si trovano già sul PLCNext della casa tedesca.
Servitizzazione. Il costruttore di macchine può vendere all’utizzatore finale una serie di servizi, che permettono ad entrambi di trarre molto valore aggiunto. La Connected Machine Web Platform di Rockwell è il punto di convergenza sul cloud per utenti e costruttori di servizi quali: manutenzione predittiva supportata da realtà aumentata, vendita e gestione dei ricambi, monitoraggio continuo e centrale delle macchine installate. «Avere una strategia IOT vincente - spiega Simone Cerizza Team Leader & Solution Consultant Smart Manufacturing e Area Project Manager MADE Rockwell «significa avere molto chiaro in mente un modello di ecosistema che comprenda non solo hedge computing e cloud ma anche block chain e intelligenza artificiale».
Come evitare nella security l’errore umano. «Nella teleassistenza / telecontrollo, riveste un ruolo fondamentale la security, che molti pensano di poter risolvere utilizzando in fabbrica prodotti non industriali» così Simone Dal Toso, Product Manager Networking Telestar. La sicurezza della connessione spesso vede contrapposti su due fronti i reparti IT e OT, che vantano grandi conoscenze nei rispettivi ambiti ma non sono sempre aperti alle esigenze dell’altro reparto. Poiché i problemi sulla security derivano sempre dall’errore umano, occorre usare prodotti semplici, impostare sempre gli accessi con 2 fattori (per es. password + dato biometrico): non esistendo un sistema sicuro al 100% è indispensabile prevedere procedure che rendano molto difficile l’intrusione.
Perché un dato viene prodotto? Perché un dato è consumato? «La risposta a queste domande - sostiene Michele Frare, General Manager Factory Automation Panasonic Industry Italia - permette di capire grazie alla verifica dell’OEE (Overall Equipment Effectiveness) se si stanno migliorando i processi (produzione, manutenzione, controllo qualità, ecc.). Tutti i miglioramenti vanno fatti in funzione del business e possono concretizzarsi con l’impiego dei nuovi dispositivi abilitanti». I dati elaborati dall’Intelligenza Artificiale e dal Machine Learning permettono di tenere sott’occhio lo stato complessivo degli impianti in tempo reale grazie alla scelta occulata di cruscotti e KPI. All’OEM si richiede oggi un salto di qualità: deve diventare, sostenuto in questo dai fornitori, specialista della connettività avanzata dal punto di vista tecnico, applicativo, di business e di formazione per i suoi end user».
Più EtherNet meno bus di campo. Per creare correttamente una infrastruttura, occorre utilizzare dispositivi industriali (cavi+connettori) in modo che i dispositivi collegati possano trasmettere i dati in modo efficiente senza rallentare il sistema. «Il pericolo - sostiene Marco Artoli, Product Manager Lapp Italia - è utilizzare metodi ottimi per l’IT ma non ideali per l’OT come ad esempio cavi o topologie lineari». Artioli consiglia inoltre di creare infrastrutture più ampie delle necessità attuali e facilmente espandibili in modo da supportare un traffico dati sempre maggiore, ricordando che Lapp porta EtherNet fino al sensore.