Percorsi di trasformazione digitale
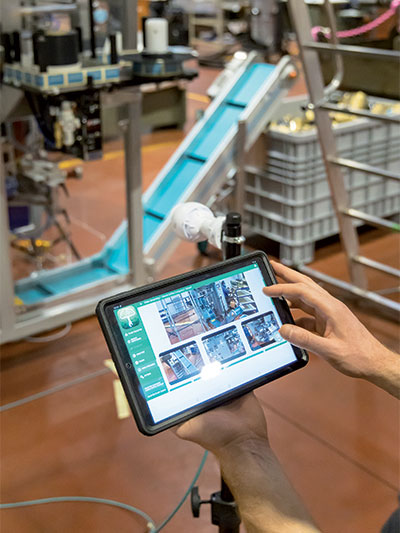
Quando un converter nonché costruttore di macchine automatiche di fama mondiale con oltre 170 anni di storia alle spalle incontra una giovane startup hi-tech, nasce una collaborazione win-win, che dà luogo a una nuova proposta di servizi. Open innovation e servitization sono i fattori chiave di un cambiamento, che consente agli utilizzatori delle macchine di migliorare produttività e flessibilità. Ce ne parlano Camillo Ghelfi e Marco Bressanello, rispettivamente CEO di 40Factory e Innovation Engineer Manager di Goglio.
Un modello di innovazione “open” è un approccio strategico e culturale in base al quale le imprese, per creare più valore e competere al meglio sul mercato, scelgono di ricorrere non più e non solo a risorse interne, ma anche a idee, soluzioni, strumenti e competenze tecnologiche che arrivano dall’esterno.
È in questo contesto che si muove 40Factory, startup hi-tech nata nel 2018, focalizzata sullo sviluppo di soluzioni Industrial IoT, in grado di accompagnare le aziende in un percorso di trasformazione digitale, consentendo loro di accedere a nuovi modelli di business per offrire prodotti più efficienti e affidabili. Ne è un esempio di successo il lavoro svolto in Goglio…
Un caso esemplare
Il Gruppo Goglio, fondato nel 1850, progetta, sviluppa e realizza sistemi di imballaggio completi, con un’offerta che si compone di imballaggi flessibili, accessori in plastica rigida come valvole e bocchelli, macchine e servizi per ogni esigenza di confezionamento. Leader di mercato nei settori del caffè, del pomodoro e delle polpe di frutta, ma anche di prodotti industriali come i granuli plastici, Goglio conta oltre 1.800 dipendenti e un fatturato di oltre 370 milioni di Euro.
Per l’azienda, la strada della competitività segue un duplice binario: quello dell’evoluzione del prodotto e quello della ricerca ossessiva dell’efficienza dei processi. In entrambi i casi, Goglio ha ritenuto che l’arma vincente fosse la trasformazione digitale: una trasformazione che ha permeato anche i prodotti, che da meccanici sono diventati sempre più meccatronici e informatici.
Sebbene le macchine Goglio si siano sempre distinte per il livello di innovazione tecnologica e le elevate prestazioni, oggi questo non basta più per rimanere competitivi e l’azienda, da qualche anno, ha deciso di puntare sull’innovazione dei servizi. Condizione base per la fornitura di servizi avanzati è la connessione delle macchine alla piattaforma cloud del costruttore, attraverso il cosiddetto Industrial Internet of Things.
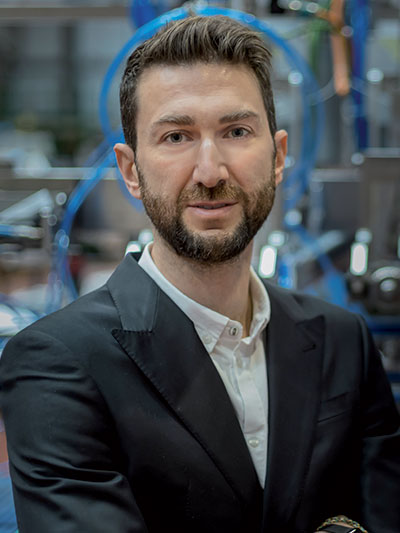
Marco Bressanello
Delle ragioni e delle prospettive aperte da questa scelta, ci parla Marco Bressanello, Innovation Engineering Manager della Divisione Macchine di Goglio.
«Il collegamento H24 consente di ricevere dalle macchine un flusso continuo di dati utili tanto al cliente quanto al costruttore. Se il primo è più interessato ai volumi produttivi di ciascun turno o al rendimento complessivo delle linee, il secondo è interessato ai dati tecnici che gli permettono di rivedere la progettazione delle macchine per migliorarne l’affidabilità e il TCO (total cost of ownership).
La nostra scelta è caduta inizialmente su una piattaforma commerciale, che però si è rivelata ben presto non perfettamente funzionale alle esigenze dell’applicazione. Goglio ha quindi deciso di sviluppare una nuova piattaforma, chiamando a collaborare 40Factory, che ha permesso di sfruttare le migliori tecnologie disponibili plasmandole sulle nostre esigenze.
A metà 2019 nasce quindi Goglio MIND, completamente rivista nella veste grafica e nelle funzionalità sviluppate.
«Il segreto di MIND è partire dalle esigenze dei clienti e arricchire costantemente la piattaforma di servizi sempre nuovi. Una delle ultime possibilità offerte consiste nel collaudo pre-consegna della macchina da remoto. In epoca di Covid, con una mobilità dei clienti ridotta e in molti casi addirittura impedita, MIND offre la possibilità di collegarsi alla piattaforma attraverso il browser e seguire il collaudo della propria macchina interagendo in tempo reale con i collaudatori di Goglio. Quattro telecamere sono contemporaneamente collegate a MIND, e il cliente, oltre a vedere i dati di velocità, tempo di produzione, confezioni prodotte e scarti, può scegliere l’immagine che desidera seguire, come se stesse assistendo a un Gran Premio di Formula 1».
L’epoca dell’istinto e delle valutazioni soggettive, d’altronde, è finita e oggi le decisioni sono data-driven, cioè prese sulla base di dati reali.
«Il flusso di dati che scaturisce dalle macchine e che viene archiviato su MIND costituisce una base che si amplia man mano, con l’aumento del numero di macchine collegate. In pratica, da questo data lake si estraggono le informazioni necessarie a consentire il progressivo passaggio da una manutenzione tradizionale a quella predittiva. «I dati disponibili vengono dunque condivisi tra costruttore e cliente - prosegue Bressanello - garantendo sempre a entrambi una visione oggettiva dei fenomeni. Inoltre, grazie alla connessione dei dati, il costruttore è in grado di offrire ai clienti servizi a valore aggiunto crescente. Tra questi, il più significativo è senza dubbio quello definito “pay per performance”, nel quale il cliente non paga per il possesso della linea produttiva, ma per i volumi di prodotto che la linea riesce effettivamente a produrre».
Goglio MIND: come funziona e cosa offre
Entriamo dunque nel merito dell’architettura e delle funzionalità della piattaforma messa a punto da Goglio, nonché dei vantaggi che ne derivano per i clienti finali.
È ancora Bressanello a tracciare i contorni di questa innovazione.
«Per i servizi digitali offerti a corredo delle linee costruite da Goglio nello stabilimento di Zeccone (PV), abbiamo collaborato con 40Factory a partire dal 2019: insieme è stato possibile potenziare la piattaforma Mind arricchendola di nuovi servizi a valore aggiunto per gli utilizzatori. Tra i clienti di Goglio figurano le principali multinazionali del caffè.
La soluzione di Industrial IoT, basata su Cloud Microsoft Azure, è costituita da una web app: con pochi click il cliente può accedere alle macchine, monitorarne lo stato di funzionamento, analizzare l’andamento di alcuni importanti KPI (key performance indicators), come l’OEE (Overall Equipment Effectiveness) e i rate di produzione, ma anche effettuare un’analisi approfondita dei fermi macchina basata su diagramma di Pareto e controllare la qualità del prodotto finito.
Non solo: la soluzione consente di archiviare lo streaming dei dati di telemetria (temperature, tensioni, assorbimento dei motori, parametri di ricetta, ecc..) in arrivo dalla macchina in un data lake ottimizzato per gestire questa funzione: a partire dai dati raccolti è possibile effettuare analisi avanzate sull’efficienza e il corretto stato di regolazione della macchina, oltre a creare le basi per logiche di manutenzione predittiva».
A quanto racconta ancora il manager «le prestazioni delle linee sono tenute sotto costante controllo dai tecnici di Goglio e non appena si riscontra un’anomalia, si interviene secondo quanto previsto dal contratto di servizio con l’utilizzatore: si va da una semplice telefonata informativa fino al supporto da remoto tramite computer o strumenti audio/video di realtà aumentata. Nei casi in cui è previsto, si organizza anche il pronto invio di un tecnico per l’intervento sul posto».
Le macchine vengono collegate alla piattaforma attraverso un piccolo box installato nel quadro elettrico, chiamato field agent. Qui i dati fluiscono direttamente dal plc di governo della macchina e subiscono una prima elaborazione attraverso metodologie di calcolo edge multilivello. Il risultato è uno stream di dati ottimizzati, pronti per essere trasferiti in cloud dove vengono elaborati. «I video e i dati raccolti sono registrati e archiviati in un’apposta sezione dell’app: la loro analisi consente lo sviluppo di funzionalità sempre nuove di miglioramento delle performance delle linee. L’efficienza viene monitorata dall’utilizzatore o, meglio ancora, dal costruttore da remoto. Un’opzione, questa, che si è rivelata fondamentale in tempi di pandemia, ma che pensiamo rimarrà nelle nostre abitudini anche quando saremo tornati alla normalità.
Da ultimo, la raccolta dei dati di produzione consente di studiare le correlazioni tra le regolazioni della macchina e le caratteristiche del materiale di confezionamento utilizzato. Dato che Goglio produce i film e costruisce le macchine, il controllo di entrambe le componenti è fondamentale per la ricerca delle condizioni che massimizzano l’efficienza complessiva del processo di confezionamento».
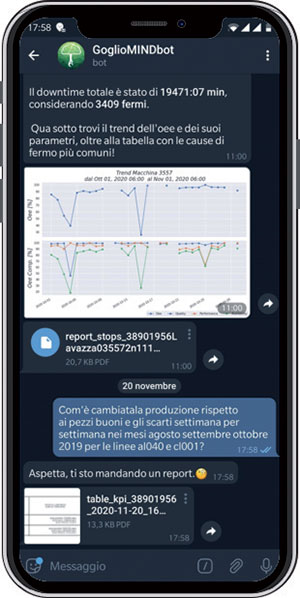
Goglio MIND BOT: l’assistente digitale che informa
La piattaforma è arricchita da un assistente virtuale, ovvero un BOT, in grado di dialogare in linguaggio naturale con gli utenti tramite diversi canali, come Telegram o web chat, così da accedere in maniera intuitiva e immediata ai dati di macchina, ai KPI e ai report di produzione.
«Gli utenti, autenticati tramite una procedura rapida e sicura - spiega Bressanello - possono porre domande anche complesse all’assistente virtuale, come per esempio “Com’è cambiata la produzione rispetto ai pezzi buoni e gli scarti, settimana per settimana nei mesi di settembre, ottobre, novembre per le linee l01, l02 e l03?”. In pochi secondi, la risposta è fornita in forma di grafico consultabile direttamente dallo smartphone. Non solo: il BOT è in grado di inviare notifiche push al verificarsi di un particolare evento critico, come un fermo macchina o il calo di efficienza sotto una soglia predefinita. Inoltre, gli utenti possono attivare la ricezione di report di produzione periodici completi, ad esempio al termine di ogni turno di lavoro».
HMI UX/I: un’interfaccia a misura d’uomo
Il processo di innovazione in Goglio non si è fermato allo sviluppo di soluzioni data driven; in un’ottica di digitalizzazione integrata, l’azienda ha deciso di rivoluzionare l’interfaccia uomo-macchina, migliorandone l’interazione e l’usabilità.
Insieme ai designer specializzati in UI/UX design di 40Factory, è stata ri-progettata un’HMI ispirata ai paradigmi del web e delle APP, caratterizzata da un numero limitato di pagine, intuitive e facilmente replicabili su modelli diversi.
«L’esigenza di compiere un simile passo - sottolinea Bressanello - nasce in primo luogo dalla trasformazione del mercato del lavoro. Ci siamo infatti resi conto che, a differenza del passato, il turnover degli operatori è molto più rapido; inoltre è sempre più difficile trovare tecnici esperti che acquisiscono una conoscenza profonda della macchina, e il tempo per addestrare le nuove leve è sempre più limitato. Considerando questo stato di fatto, abbiamo deciso di reingegnerizzare l’HMI in termini innovativi, in modo da eliminare le “incomprensioni” tra macchina e operatore, riducendo errori e tempi di apprendimento; questo ci ha consentito, inoltre, di rendere immediatamente riconoscibili le nostre macchine, in un’efficace operazione di branding. Del resto, l’interfaccia è l’elemento di interazione con la macchina e un’HMI curata anche nei dettagli non può che conferire ulteriore valore a un prodotto già eccellente in partenza, facilitandone l’uso e migliorando la produttività dell’impianto».
In conclusione, risultati e prospettive
In sintesi, ragionando sulle informazioni ricevute dai nostri interlocutori possiamo dire che le tecnologie disponibili evolvono rapidamente, e per integrarle nel modo corretto e poterle sfruttare è richiesto un notevole sforzo. Il vantaggio però è evidente: grazie all’utilizzo di questi strumenti cambia profondamente la natura del rapporto tra costruttore e cliente finale. Entrambi arrivano a parlare “la stessa lingua”: un linguaggio basato su dati e non su opinioni, che consente di avviare partnership più strette, con obiettivi comuni più facilmente raggiungibili.
Goglio crede che questa sia la direzione giusta, e sebbene il passaggio si prospetti graduale, pensa già a un futuro dove tutte le macchine, a prescindere da costruttore e caratteristiche, saranno connesse: in questo modo, interagire con piattaforme di questo tipo, dialogare con un assistente virtuale e avere un facile accesso a dati e KPI per l’intero ciclo di vita delle macchine diventerà la quotidianità.
40Factory e l’approccio verticale a Industry 4.0
Nata nel 2018, la startup hi-tech 40Factory opera nei settori dell’industria 4.0 e della digitalizzazione di macchine e impianti industriali.
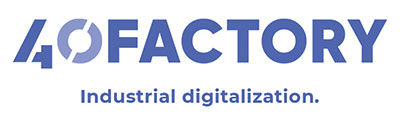
L’azienda è specializzata nella gestione di tutti i livelli tecnologici coinvolti in un progetto di digitalizzazione: dalla connettività di sensori, macchine e impianti, fino all’integrazione con i sistemi di controllo e pianificazione della produzione già implementatati dal Cliente (MES, ERP), con l’obiettivo di estrarre dati, ricavarne informazioni (presentandoli tramite web app caratterizzate da UI e UX avanzate) e, soprattutto, valore grazie all’intelligenza artificiale.
Le attività svolte nel corso dello sviluppo di un progetto hanno un impatto progettuale, tecnologico e anche consulenziale: ciò grazie alla combinazione di competenze IT e conoscenza del mondo OT che caratterizza le risorse tecniche che collaborano in azienda.
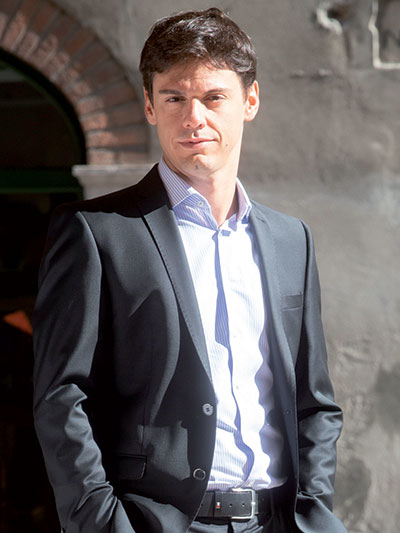
Camillo Ghelfi
Di come 40Factory opera in questo complesso “ecosistema”, ce ne parla il CEO, Camillo Ghelfi (nella foto): «Noi mettiamo a disposizione le nostre competenze in un’ottica di collaborazione win-win con le aziende partner, come ad esempio Goglio, consentendo loro di accedere alle innovazioni disponibili sul mercato per integrarle con il proprio modello di business. In questo modo, le aziende non sono costrette a realizzare al proprio interno ogni innovazione, ma sono libere di modulare in modo efficiente ciò che “viene da dentro” e ciò che è possibile ricavare da player esterni, guadagnando in competitività».
Una strategia che, anche in riferimento al settore del packaging, si sviluppa su obiettivi specifici, come ricorda ancora Ghelfi.
«Lo scopo finale resta quello di consentire alle aziende di rispondere alle esigenze di flessibilità e di volumi di produzione richiesti dal mercato. Tali obiettivi si declinano, dal punto di vista di un OEM, nella possibilità di offrire macchine affidabili, efficienti e più produttive, caratteristiche che consentono poi all’utilizzatore finale di ottimizzare il time-to-market e la capacità di ampliare la gamma dei prodotti.
Approfondendo poi il modello di business, il punto di arrivo è l’accesso alla servitizzazione, ossia il passaggio dalla ownership (e quindi dalla vendita di un prodotto fisico) alla usership, ossia alla cessione di un servizio, dove la macchina resta protagonista, ma non viene più descritta solo attraverso le sue caratteristiche fisiche bensì tramite le sue capacità produttive, misurabili e garantite grazie a data analytics e AI».
Driver tecnologici abilitanti, che generano valore
In questo momento storico, d’altronde, appare evidente come la leva di crescita per l’industria manifatturiera non sia più (esclusivamente) la “macchina” considerata dal punto di vista ingegneristico; determinanti sono anche i modelli organizzativi, i dati, l’intelligenza artificiale... Il che significa che il vero vantaggio competitivo è legato alla capacità di estrarre dal dato un’informazione, e quindi un valore. In altri termini, è possibile definire una “catena di valore del dato” che parte dal dato grezzo, oggi disponibile in grandi quantità, ma che a sua volta deve essere elaborato e trasformato in informazione.
«Ecco perché lo scopo finale del percorso che imbocchiamo con le aziende partner è di portarle a generare valore, assumendo il dato come base sul quale fondare decisioni sia operative che strategiche. Ma per avere successo in questo iter di trasformazione - sintetizza Ghelfi - è necessario implementare tecnologie che consentano di acquisire, elaborare e archiviare i dati, così da renderli facilmente fruibili dagli utenti. Edge e cloud computing sono i due layer tecnologici fondamentali che si inseriscono nella Data Value Chain. Se il cloud computing è sempre più diffuso e offre importanti benefici (pensiamo alla disponibilità di uno spazio di archiviazione flessibile e semplice da mantenere, all’accessibilità da remoto, all’ottimizzazione delle politiche di cybersecurity garantita da grandi provider come Google, Amazon, Microsoft, Siemens… ), l’edge computing rappresenta oggi una tecnologia matura, ma non sempre pienamente sfruttato. Si tratta infatti di un livello di elaborazione intelligente, capace di garantire potenza di calcolo a bordo macchina, deputato a pre-aggregare e archiviare i dati nonché fondamentale per l’esecuzione di algoritmi di AI, vero valore aggiunto delle soluzioni 40Factory.
Tale livello, inoltre, consente non solo di ottimizzare l’utilizzo del cloud, ma permette anche di usufruire delle soluzioni IoT in “versione on-premise”, utile soprattutto in quei contesti in cui il cloud non è utilizzabile o in cui è richiesto confinare i dati entro l’organizzazione del cliente».
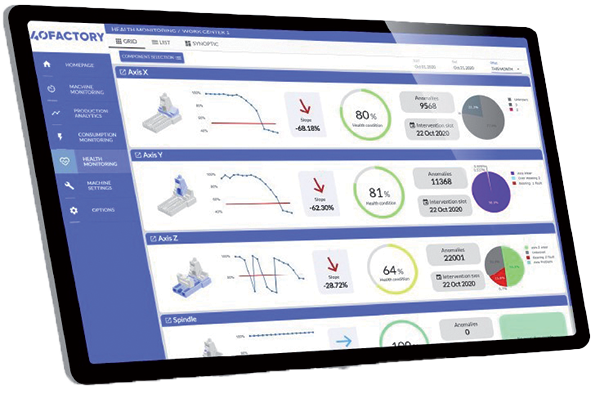
Machine Analytics Tool
La soluzione integrata di 40Factory per la manutenzione predittiva
Il prodotto di punta di 40Factory è Machine Analytics Tool (MAT): si tratta di una soluzione IoT che sfrutta tecnologie innovative come Machine Learning e Deep Learning, adatta sia a costruttori di macchine che end user che puntano a realizzare un condition monitoring avanzato del proprio parco macchine o di asset strategici.
Essa, infatti, consente agli utenti di monitorare da un unico punto di accesso lo stato di ogni macchina e impianto industriale connesso, di analizzare KPI di efficienza e di produzione, di esaminare i consumi energetici e, soprattutto, di rilevare in anticipo grazie all’AI comportamenti anomali dei componenti macchina per prevedere il verificarsi di guasti e breakdowns. In poche parole: rende le macchine più intelligenti.
La piattaforma è pensata per essere accessibile in modo rapido e sicuro tramite una web app strutturata in moduli e dashboard facilmente comprensibili e informativi anche per chi non è in possesso di approfondite competenze nella data analytics. Inoltre, la soluzione è anche proattiva: tramite un sistema di avvisi è in grado di notificare (via mail o integrandosi con un chatbot implementato in chat telegram o canali Teams) agli utenti l’avverarsi di eventi configurabili tramite l’interfaccia web, come ad esempio il livello di salute di un componente di automazione sotto una soglia limite per un “tempo x”.
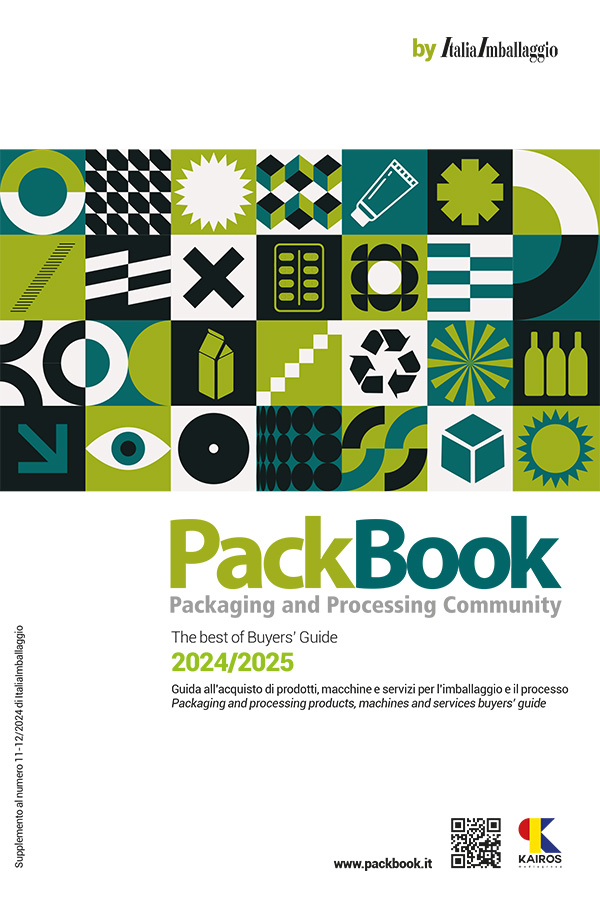