Scelte di crescita, step by step
Robopac Smart Factory è un progetto in divenire. Dalla revisione del layout produttivo dello stabilimento Robopac Machinery di San Marino fino all’integrazione delle tecnologie I4.0 destinate a migliorare l’efficienza dei processi: un modello da replicare in ottica di Gruppo.
Motivato dall’esigenza di incrementare la produzione e dall’opportunità di cogliere appieno il trend di un mercato in forte crescita, il progetto “Robopac Smart Factory” ha preso avvio dallo stabilimento Robopac Machinery di San Marino nel 2018. Primo step della collaborazione tra Porsche Consulting e i giovani e preparati ingegneri del team Robopac: la revisione del layout produttivo dello stabilimento, cui è seguita la selezione delle tecnologie digitali da adottare.
«Il nostro obiettivo era migliorare ulteriormente flessibilità ed efficienza dei processi - dichiara Enrico Aureli, CEO di Robopac - oltre a prevedere un aumento del 50% della capacità produttiva del plant di San Marino. Vogliamo arrivare al top dell’automazione e della digitalizzazione, continuando però a valorizzare le persone, che rimangono al centro della nostra strategia imprenditoriale… Perché se la tecnologia ci aiuta a massimizzare produttività e flessibilità, assicurando una capacità di analisi rapida e approfondita, è pur sempre l’intelligenza umana a programmare e ottimizzare tutti i processi».
Per sviluppare il progetto “Smart Factory” sono stati scelti partner tecnologici di primo livello, anche in ottica di Gruppo, per poi mutuare i risultati ottenuti, nel tempo, in tutti gli stabilimenti. Dopo l’impianto pilota di San Marino, infatti, tutti gli altri plant saranno coinvolti in un processo di ulteriore automazione e digitalizzazione, ognuno a seconda delle proprie caratteristiche.
Investire nel miglioramento continuo
Il progetto Smart Factory non nasce all’improvviso, ma è il risultato degli investimenti costanti che hanno consentito a Robopac di raggiungere standard operativi allineati ai più moderni canoni di produzione. Ricordiamo al proposito, l’introduzione nel “lontano” 2008 - e in una fase congiunturale negativa, dunque - delle metodologie della Lean Production, messe in atto con successo a garanzia di una completa customer satisfaction: riduzione del Time To Market; trasparenza nel visualizzare lo stato di avanzamento della commessa, garantendo la certezza della consegna; incremento della qualità intrinseca del prodotto…
Risale invece al 2011 la realizzazione del nuovo stabilimento di Robopac Machinery a San Marino, altra tappa fondamentale del percorso aziendale orientato a innalzare capacità produttive, efficienza e qualità a sostegno di una competitività capace di generare profitto e alimentare i piani di crescita.
Nel 2018, supportati dal robusto aumento dei volumi di fatturato e da un mercato che apriva ulteriori spazi di sviluppo, con una capacità sfruttata quasi al limite e analizzando l’orizzonte temporale di 3-5 anni, si è quindi valutato che la Lean Production fosse ormai diventata patrimonio culturale dell’azienda. Ed era il momento di coniugarla ai concetti di Industry 4.0, promuovendo un ulteriore step organizzativo, necessario e decisivo per la completa automazione e digitalizzazione della fabbrica.
Verso la Smart Factory
Il progetto “Robopac Smart Factory” ha quindi potuto prendere avvio con una revisione complessiva del layout e dei processi nell’ottica dell’ampliamento della capacità produttiva e dell’integrazione delle tecnologie digitali. È stata compiuta un’analisi preliminare delle tecnologie più adatte per essere introdotte all’interno dei processi esistenti, così da raggiungere gli obiettivi prefissati. Oltre alla nuova disposizione dei reparti e della logistica, sono stati quindi selezionati tre progetti digitali da inserire nel processo, individuando le partnership migliori.
Che succede negli altri stabilimenti italiani del Gruppo? I principi della Lean Production sono già attuati anche negli altri stabilimenti italiani del Gruppo. A Castel San Pietro Terme (Bologna) - quartier generale di Robopac dal 2018 - dove si producono le macchine automatiche Dimac (Robopac Packers), l’impianto è dotato di una linea motorizzata ed è già predisposto sul fronte delle infrastrutture per ulteriori step di ammodernamento e digitalizzazione, che inizierà dalla parte logistica. Anche lo stabilimento Robopac Systems di Villa Verucchio (Rimini) e lo stabilimento OCME di Parma, grazie alla collaborazione dei partner tecnologici del Gruppo già individuati, completeranno il proprio percorso verso la Smart Factory nell’arco del triennio 2021-2024. |
Il progetto complessivo, realizzato ancora una volta con il prezioso contributo di Porsche Consulting, è stato in seguito implementato e portato avanti dal Kaizen Department di Robopac, un team strutturato e dotato di competenze specialistiche in relazione alle tre aree: Manufacturing, MES Automation e Logistics.
Il nuovo Logistic Hub. Nel 2019 è stata avviata la ristrutturazione del plant Robopac Machinery di San Marino, aggiungendo una nuova area di circa 3.000 mq, in pratica attigua al sito principale di 15.000 mq, da cui dista solo 2 km. L’area è stata destinata al Logistic Hub, polo logistico asservito da una navetta, che vi trasferisce tutta la produzione proveniente dal sito principale, prima delle spedizioni worldwide. Al contempo, nel sito principale sono stati modificati i layout dei due piani produttivi e definite le tecnologie digitali: AGV, MES e WMS.
Introduzione degli AGV. Forte della partnership con l’azienda Scaglia Indeva, per la logistica interna della Linea 1 - la linea principale che si trova al piano zero dello stabilimento, in grado di produrre una macchina ogni 13 minuti - sono stati introdotti i veicoli a guida automatica (AGV). È stata raddoppiata la superficie della linea di montaggio, in precedenza motorizzata, con l’aggiunta di 26 AGV per una differente movimentazione delle macchine, gestita interamente da un sistema centrale. Grazie a questa innovazione, ogni macchina, a seconda della tipologia e delle caratteristiche desiderate, è in grado di prendere percorsi diversi a seconda delle lavorazioni necessarie. Il sistema fornisce per ogni singola macchina le informazioni del caso all’operatore nella postazione di lavoro di destinazione. Una volta terminata e collaudata, la macchina viene poi ricondotta automaticamente nel flusso principale e da lì all’area di spedizione, completando il circuito.
Si tratta della linea più interessante e tecnologicamente all’avanguardia di tutto il Gruppo, in quanto rivoluziona la logica delle linee di montaggio tradizionali. Introduce infatti il concetto molto moderno dei percorsi variabili a seconda della tipologia di macchina da produrre, avvalendosi di un sistema avanzato di automazione e movimentazione… un fiore all’occhiello nel mondo delle macchine packaging ma non solo. Il sistema di supervisione degli AGV si interfaccia inoltre con il sistema MES per gestire al meglio il flusso produttivo.
Il Manufacturing Execution System. In collaborazione con Siemens, Robopac ha introdotto il sistema di gestione della produzione e raccolta dati MES (Manufacturing Execution System), che assicura standard di qualità ed efficienza integrati nel processo di produzione, applicati in modo proattivo e sistematico. Il sistema si integra facilmente con apparecchiature, controller, applicazioni aziendali e per il ciclo di vita del prodotto, sistema di gestione della qualità e dei laboratori e numerose altre applicazioni. I risultati sono visibilità completa, programmazione, controllo e ottimizzazione della produzione e dei processi in tutta l’azienda. Un vero e proprio prototipo di integrazione totale, in quando, come precisato, è in grado di interfacciarsi anche con il sistema degli AGV.
La logistica di magazzino. Replica Sistemi (Zucchetti Group) ha implementato anche un software specifico per la gestione della logistica di magazzino, integrato all’add-on WMS Analytics per effettuare analisi visive immediate dei dati e delle prestazioni. Anche questa soluzione è interamente integrata con il gestionale SAP e il MES.
Una fabbrica digitale e integrata
Alla conclusione del progetto, prevista a fine 2020, la fabbrica Robopac Machinery di San Marino sarà completamente digitale e integrata. Nella Linea 1, dove il sistema MES è già operativo, sono stati installati 30 pannelli digitali touch screen per lo scambio dei dati operativi tra gli operatori, che illustrano tempo reale ciò che sta accadendo nell’impianto. Entro la fine dell’anno il MES sarà in funzione su tutte le 5 linee di montaggio, così come nel reparto logistico.
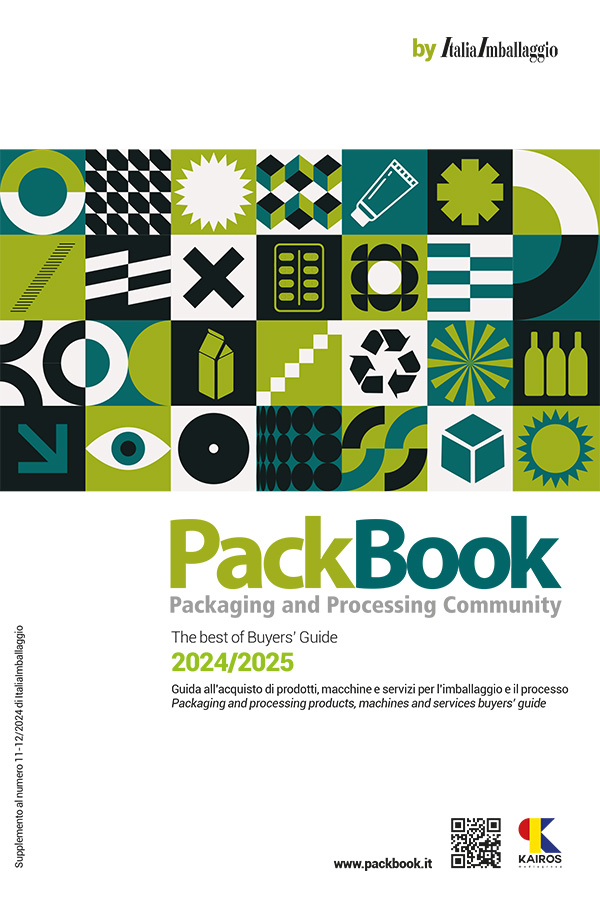