Strato su strato fino alla meta
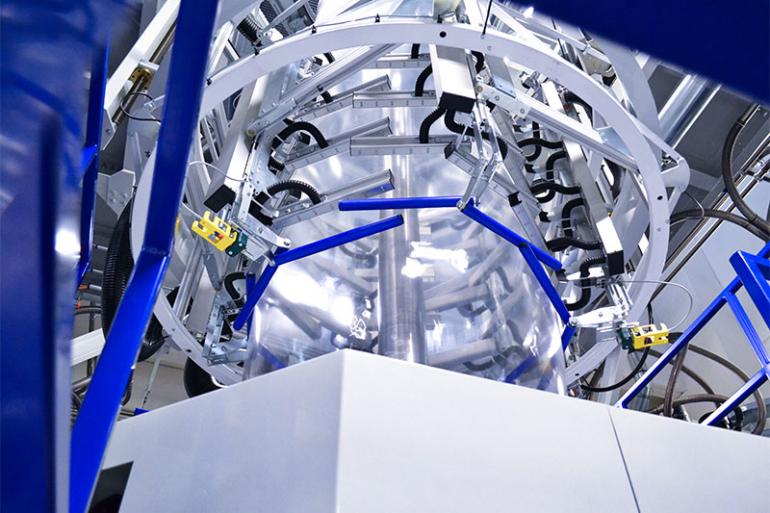
Sostenibilità ambientale ed economica significa, anche, avere un film da imballaggio da 30 micron al posto di uno da 50 micron. Oggi è infatti possibile risparmiare fino al 25% di materiale - con impianti di estrusione in bolla a 27 strati della GAP - ma è ancora forte il timore di “cambiare” da parte dei converter e, soprattutto, dei brand owner che fanno il mercato. Eppure la strada che passa dalla riduzione degli spessori dei materiali e dal miglioramento delle loro caratteristiche funzionali e barriera è inevitabile: parola di chi sa non solo costruire gli impianti, ma anche produrre i film.
Stefano Lavorini
Tutte le strade portano a Roma, si dice… che, tradotto, per un imprenditore suona: arrivare a vendere belle macchine e avere clienti contenti.
La via percorsa da GAP parte dall’attività di engineering, passa dalla progettazione e costruzione di impianti di estrusione/soffiaggio (doppia e multi bolla) per poi ampliarsi - prendendo spunto dall’attività di R&D - alla produzione di film termoretraibili barriera per il confezionamento di carni e formaggi.
Oggi, il senso di questo percorso, che ha permesso di combinare know-how ed esperienze nel campo delle macchine e dei materiali, trova la summa nella realizzazione di un impianto di soffiaggio in bolla dotato di testa di coestrusione circolare con tecnologia microlayer e 9 estrusori, per la produzione di film poliolefinici con struttura fino a 27 strati.
Un’innovazione che promette - rispetto agli impianti attualmente commercializzati - di offrire notevoli vantaggi, ovvero di realizzare film barriera più sostenibili, nonché più economici, per buste stand-up, per top di vaschette, per la laminazione, per il confezionamento skin e per numerose altre applicazioni.
Più strati, meno costi

La moltiplicazione degli strati e la combinazione di diversi polimeri con differente viscosità e temperature di processo in un singolo film consente di avere un prodotto finale con caratteristiche meccaniche superiori e un minore spessore. Con la tecnologia microlayer messa a punto da GAP è possibile migliorare le proprietà fisiche dei film poliolefinici e quindi diminuirne del 20-25% lo spessore, nonché aumentare il contenuto di polimero riciclato.
In questo modo si riducono i costi, utilizzando meno materiale, e si risparmia sul contributo CONAI e sull’imminente Plastic Tax.
Un bel risultato, quindi, perfettamente in linea con la crescente attenzione alla sostenibilità degli imballaggi.
E che non si tratti di solo di una bella idea ma di una realtà concreta, lo dimostra l’impianto in funzione presso il centro di R&D dell’azienda di Trecate (NO), dove è possibile, grazie ai 3 speciali feed block, realizzare formulazioni dei film illimitate, alternando fino a 9 diversi tipi di polimeri in modo sequenziale o alternato.
Tra i tanti vantaggi, la riduzione di spessore degli strati barriera (tipicamente EVOH) così da ottenere imballi riciclabili, ma anche la realizzazione di strutture biodegradabili, compostabili e marine-compostable.
D’altronde, se da una parte non si fa altro che parlare di economia circolare, di riduzione in peso degli imballaggi e della loro riciclabilità (industriale), di abbattere i consumi energetici e le emissioni di CO2, dall’altra è fuori discussione che ci sia ancora molto da fare per cambiare approccio e modo di guardare al proprio business. Cosa, evidentemente, più facile a dirsi che a farsi.
Eppure le buone ragioni, come in questo caso, non sembrano proprio mancare.
L’impresa è vincere la resistenza al cambiamento che è connaturata alla natura umana: questo significa per i converter promuovere l’innovazione presso i propri clienti, superando la logica del “prezzo al chilo”, e per i brand owner modificare i capitolati di acquisto, per migliorare il proprio bilancio di sostenibilità, spendendo meno per il materiale da imballaggio.
Una vita da film
