Magazzino ricambi: come ridurne le voci di costo
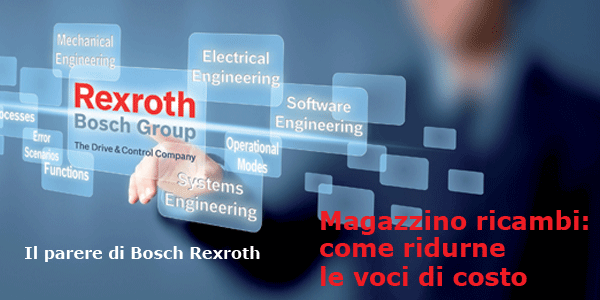
L'ESPERTO RISPONDE Luca Stanzani (Packaging and Processing Bosch Rexroth Italia) risponde ai quesiti posti dai lettori, circa le problematiche tecnologiche e di mercato relative all’automazione. Dalla rubrica pubblicata su ItaliaImballaggio di maggio 2013.
Domanda
Buongiorno, più che una domanda le vorrei segnalare una necessità che accomuna la maggioranza degli end user. Le nostre linee di produzione sono caratterizzate da impianti e macchine realizzati da fornitori vari che spesso utilizzano sistemi e prodotti diversi. Per evitare fermi macchina siamo costretti ad avere magazzini di ricambi immensi, che hanno un impatto devastante sui costi. C’è una soluzione a tutto questo? R.R.
Purtroppo non esiste una risposta che possa risolvere completamente il problema. Il primo suggerimento è, comunque, cercare di ridurre i codici a magazzino e i capitali immobilizzati evitando le obsolescenze.
Ma come fare? Ecco alcuni semplici consigli:
• allacciare un rapporto aperto e attivo sia con i fornitori di macchine che di componenti;
• richiedere ai costruttori la lista dei ricambi consigliati;
• avere le previsioni aggiornate di phase out dei prodotti. per evitare, prevenire e gestire eventuali obsolescenze;
• richiedere ai fornitori degli impianti di standardizzare il più possibile i componenti presenti; infatti con un minimo sforzo è molto spesso possibile ridurre anche del 30-40% il numero di codici movimentati (gli esempi più ricorrenti sono la taglia e le opzioni di motori, riduttori, attuatori pneumatici, attuatori lineari, etc). A questo proposito vorrei portare un esempio che ci ha coinvolto di recente. Bosch Rexroth è riuscita ad aggiudicarsi un importante nuovo cliente grazie all’offerta di guide lineari che garantiscono gli stessi carichi su tutti i 4 lati e la classe di tolleranza anche con componenti sciolti (e quindi non legate alla fornita abbinata guida/pattino); tutto questo ha permesso una maggior standardizzazione dei componenti e una riduzione dei codici del 40%;
• utilizzare prodotti flessibili (ad esempio, la gamma Rexroth Indradrive offre un unico hardware che può funzionare sia da inverter che da servo, con o senza retroazione);
• proporre, laddove possibile, l’utilizzo di standard internazionali (da evitare le personalizzazioni) e l’intercambiabilità dei componenti (guide, pattini, cilindri pneumatici ISO, moduli I/O’s, motori asincroni);
• richiedere l’utilizzo di prodotti e sistemi che possano essere utilizzati con sistemi e protocolli diversi.
In relazione all’ultimo punto, segnaliamo due importanti innovazioni introdotte da Bosch Rexroth nella gamma di inverter e servo azionamenti, che hanno come obiettivo la standardizzazione degli hardware e firmware con conseguente riduzione dei codici movimentati.
In particolare, facciamo riferimento all’introduzione e all’utilizzo di ingressi multi encoder - cioè un’unica interfaccia di acquisizione encoder, e quindi un unico codice, che permette di gestire encoder (motore e/o esterni ) con i protocolli più comuni in uso (Hiperface®, EnDat 2.1, EnDat 2.2,1 Vpp, 5 V TTL, Resolver) - e di una interfaccia di comunicazione multiprotocollo, cioè un unico supporto (hardware e firmware) e quindi un unico codice, che supporta quattro diversi standard di comunicazione basati su protocollo Ethernet (SERCOS III, PROFINET IO (RT), EtherNet/IP, EtherCAT).
Entrambe le innovazioni rispondono esattamente alla necessità di ridurre i codici a magazzino. Di fatto, un unico hardware, in grado di dialogare con 4 protocolli di comunicazione diversi e leggere 6 differenti tipologie di encoder, riduce potenzialmente del 95% i codici movimentati (in pratica si passa da 24 codici a un unico e solo modello).
Infine vorremmo aggiungere alcuni spunti per gli end user, sulla base dell’esperienza consolidata nel corso degli anni durante le consulenze e i servizi post vendita elaborati e forniti nei vari stabilimenti di produzione.
È fondamentale conoscere i prodotti installati sui propri impianti. Con una semplice mappatura dell’installato (l’operazione può essere eseguita una tantum) è possibile avere un quadro chiaro e completo dei prodotti e dei sistemi installati o, per lo meno, di quelli più strategici e sensibili. Incrociando queste informazioni con le scorte a magazzino è immediato riscontrare la mancanza di alcuni ricambi strategici o riconoscere eventuali situazioni di obsolescenze e sovra stock (situazioni assolutamente non così rare come si potrebbe pensare).
Infine mantenere una tracciabilità di rotture, riparazioni e sostituzioni è un ottimo modo per monitorare, anche attraverso lo storico e la statistica, le criticità a cui porre maggior attenzione.
Per avere un parere dall’esperto Bosch Rexroth, invia le tue richieste a [email protected]
For further information www.boschrexroth.it