Logica di filiera tra sostenibilità e innovazione
Marcatura e tracciabilità, qualità ed estetica del confezionamento, handling che guarda all’integrità del prodotto: da ACMA una serie di risposte che fanno della cura del dettaglio e del dialogo tra i protagonisti della supply chain la chiave del suo percorso di sostenibilità e digitalizzazione.
Luciana Guidotti
ACMA, azienda del Gruppo Coesia, è un’impresa che ha “fatto la storia” del packaging e oggi è pronta alle nuove sfide - sostenibilità e materiali innovativi in primis - che il settore deve affrontare.
Leader nella progettazione e produzione di macchine per il confezionamento, esporta circa il 95% delle soluzioni, ha più di 250 dipendenti e investimenti in R&D pari al 5% del fatturato, con una particolare focalizzazione sui mercati confectionery, saponi, detergenti e tè.
Delle novità finalmente live in fiera a Ipack-Ima e della visione di un mercato complesso come quello del biennio 2020-2022, ha parlato a Italiaimballaggio Roberto Lattarulo, Marketing Manager ACMA.
Novità che rispettano tracciabilità ed estetica
«ACMA ha portato tre soluzioni dedicate al confectionery» racconta Roberto. «Due macchine già in portafoglio per il wrapping del cioccolato e l’unità Material Gate, un sistema messo a punto dal nostro reparto R&D che consente di svolgere test su materiali di qualunque natura, per provarne le performance su un incarto con twist, ad esempio il doppio fiocco.
Partiamo dalla CW 800 per il wrapping del cioccolato sferico o a ovetto, che gestisce incarti a doppio fiocco o del tipo rullato su base alluminio. Nella nuova versione è attrezzata con un marcatore laser, in grado di stampare in maniera non appariscente ma leggibile, qualunque stringa alfanumerica si voglia su ogni singolo incarto. In questo modo il cliente è in grado di indicare lotti e scadenze non solo sul packaging secondario ma anche su quello primario, senza inficiarne l’estetica».

«Passando alla CW 600 - prosegue Lattarulo - si tratta di una macchina molto versatile per prodotti a base piana che, a una velocità fino a 600 pezzi al minuto, incarta cioccolatini con diverse fogge (fino a 6 tipologie). A Ipack Ima abbiamo deciso di mostrare l’ultimo stile sviluppato per questa macchina, il portafoglio con fascetta. La novità è duplice: il tipo di incarto particolarmente ricercato e OptiMate, il nostro pannello HMI smart sviluppato insieme a Coesia, installato su hardware proprietario del gruppo Coesia».
In un mercato dove le difficoltà di approvvigionamento di semiconduttori e componenti sono evidenti, il gruppo Coesia può contare su una propria catena di fornitura, che permette oggi ad ACMA di estendere la nuova soluzione HMI a numero crescente di macchine, dotandole di interfacce ergonomiche con grandi doti di reattività e di capacità di elaborazione.
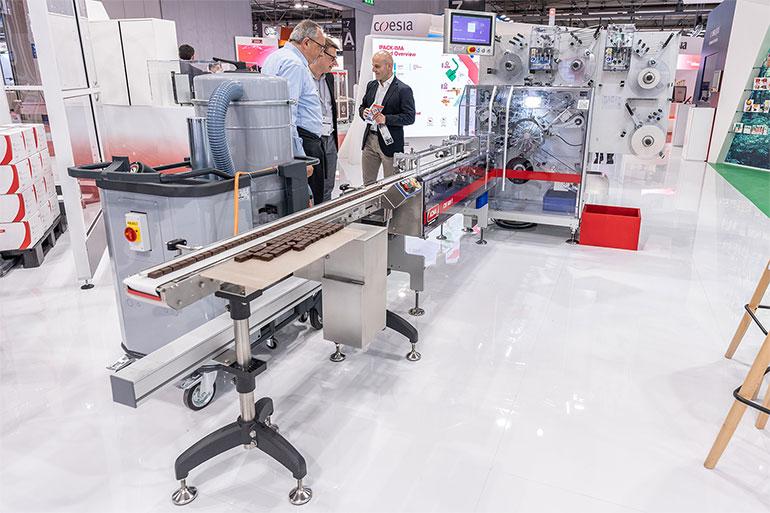
Materiali innovativi senza segreti con Material Gate
«Parte del Sustainability Lab, la terza soluzione esposta è Material Gate, un’unità di test innovativa realizzata ad hoc dagli ingegneri di ACMA per svolgere prove su materiali di qualunque natura, verificandone le performance su un incarto con twist» racconta ancora Lattarulo.
«In termini generali, il mercato confectionery si sta orientando verso la riduzione dei materiali a base plastica o multistrato, il che impone ai costruttori di macchine di trovare soluzioni efficaci in termini di produttività ed estetica nell’utilizzo di materiali alternativi».
E prosegue: «Grazie a un gruppo servomotorizzato collegato a un computer, il nostro Material Gate permette di impostare diverse leggi di moto per testare i materiali e misurarne le performance come se si fosse in un contesto produttivo reale».
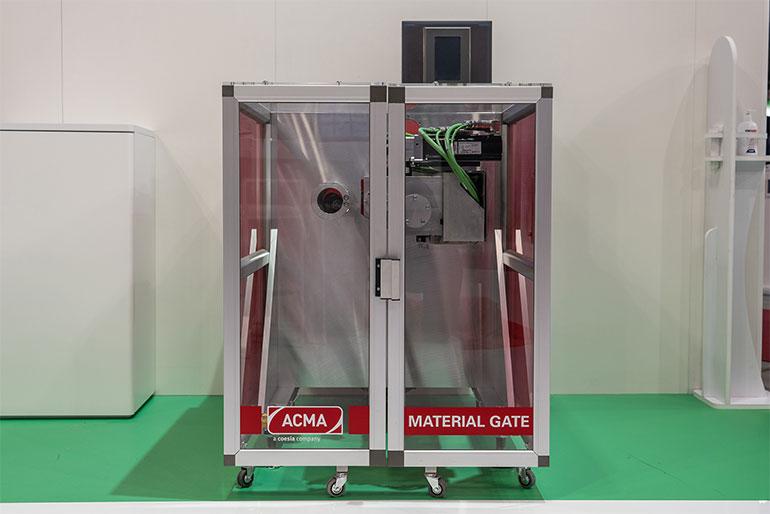
Sempre più green
ACMA ha peraltro da tempo dato vita al Sustainability Lab, che ha proprio il compito di verificare il comportamento e la macchinabilità dei materiali di nuova generazione, sia per incarti di tipo flowpack sia per il wrapping, con particolare attenzione a quelli dove il twisting può creare delle criticità.
«Il laboratorio esegue inizialmente l’esame dei materiali proposti dai clienti o dai produttori di incarti, offrendo un feedback preliminare: se positivo, il materiale può essere testato. Inizia, quindi, una prima fase di approfondimenti da parte del Coesia Engineering Centre (CEC), che ne studia le caratteristiche in funzione dell’applicazione finale e lo confronta con il “best in class”, in accordo con le nostre conoscenze, definendo così un Delta Report ad hoc.
In una seconda fase il materiale viene direttamente provato su una flowpack dedicata oppure, per gli incarti twist, ad esempio il doppio fiocco, utilizzando Material Gate, procedendo così alla messa a punto del materiale, nel caso di un produttore, o della macchina se si tratta di un produttore.
Seguendo questo processo si arriva in produzione con un materiale realmente adeguato alle esigenze e senza un oneroso spreco di prodotti».
«Un processo a fasi - precisa ancora Lattarulo - che permette di implementare nuovi prodotti nonché di modificare la nostra offerta, anche in termini di aggiornamento e retrofitting di macchine esistenti, rafforzando così la portata delle nostre scelte di sostenibilità. Le macchine ACMA, ancora oggi, sono in parte basate su movimenti meccanici che, almeno secondo gli standard tecnologici attuali, continuano a garantire precisione e velocità elevate. In sintesi, puntiamo a supportare i clienti in questo momento di transizione epocale e ad acquisire un know-how per lo sviluppo delle macchine del futuro».
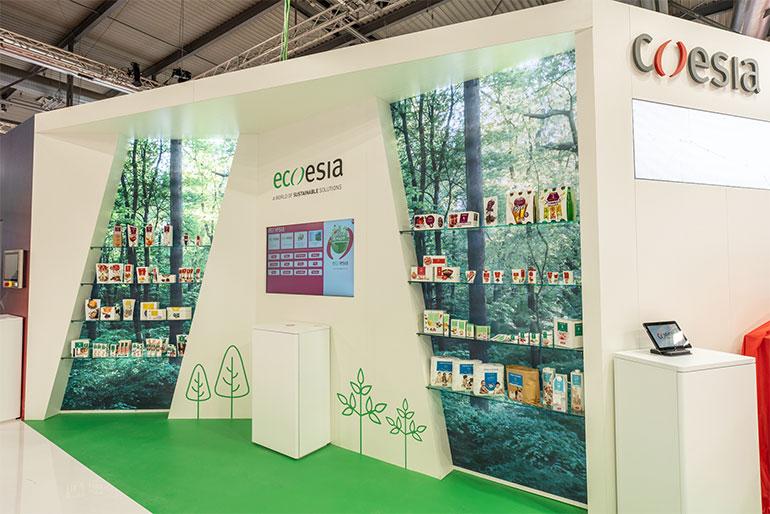
Qualità, Industry 4.0 e cybersecurity
«Il mondo va verso una personalizzazione e una flessibilità di massa. Tutti vogliono essere assolutamente unici» chiosa Lattarulo. «È chiaro che la produttività della macchina è strettamente legata al ritorno sull’investimento, inteso come affidabilità tecnica, velocità costante nel tempo e qualità dell’incarto. ACMA è riconosciuta globalmente proprio per questi valori: che si tratti di confectionery, sapone o tè, sono infatti la cura del prodotto, il suo handling, a fare la differenza, specialmente in mercati come quelli del cioccolato e del sapone, dove questo aspetto è particolarmente critico».
Qualità è indiscutibilmente coniugata alla flessibilità, che permette ad esempio di garantire cambi formato rapidi sulla stessa macchina, rafforzando il ritorno sull’investimento e riducendo gli spazi occupati in fabbrica».Dice ancora Lattarulo: «D’altronde, oggi puntiamo a una macchina sempre più “smart”: con OptiMate, il pannello connesso, acceleriamo e agevoliamo operazioni come il cambio formato guidato, la risoluzione di problematiche di macchina, la manutenzione, la formazione dei tecnici, l’accesso alle procedure e alla documentazione digitale direttamente sulla macchina. Ambiamo, poi, a connettere il parco macchine e le linee di produzione con PerforMate, la piattaforma IioT sviluppata con Coesia, che ne consente il controllo remoto per identificare problematiche, seguire le performance e avere il pieno controllo dell’attività in fabbrica. Guardando all’operatore, inoltre, maggiore connettività significa anche maggiore ergonomia, in un quadro operativo molto più intuitivo e sicuro. La parte della sicurezza è ovviamente basilare: se una macchina non è sicura non esce dallo stabilimento ACMA».


Per restare in tema industry 4.0, con UltiMate, anche la fase di manutenzione predittiva è oggetto di una specifica offerta.
«Si tratta di soluzioni sul mercato da tempo e dimostrano come i concetti di digitalizzazione della produzione si stiano consolidando. OptiMate, ad esempio, è disponibile su diversi modelli ACMA come la CW 800, la HW 900, la JW700 e ora anche su CW 600; PerforMate ha già trovato diverse applicazioni, mentre UltiMate sta per essere fornito a uno dei tanti e consolidati clienti ACMA».
Queste innovazioni impongono la massima attenzione alla cybersecurity e, per questo, l’azienda bolognese sta portando avanti una serie di assessment con enti certificatori esterni, allo scopo di garantire la sicurezza dei sistemi sviluppati.
«Con Remote Assistance di Coesia, chiudiamo il cerchio» conclude Lattarulo «Nasce come un servizio per fare assistenza remota ai nostri clienti, facendo risparmiare tempo e risorse, e anche per guidarli nel fine tuning, grazie all’uso di tecnologie di condivisione audio e video avanzate. Queste stesse tecnologie sono state poi utilizzate durante l’emergenza COVID-19 e ci hanno consentito di dare supporto ai nostri clienti e garantire una continuità di business altrimenti impossibile. Un esempio su tutti: il Factory Acceptance Test (FAT) da remoto, che è ormai una realtà entrata in pianta stabile nei nostri processi aziendali».
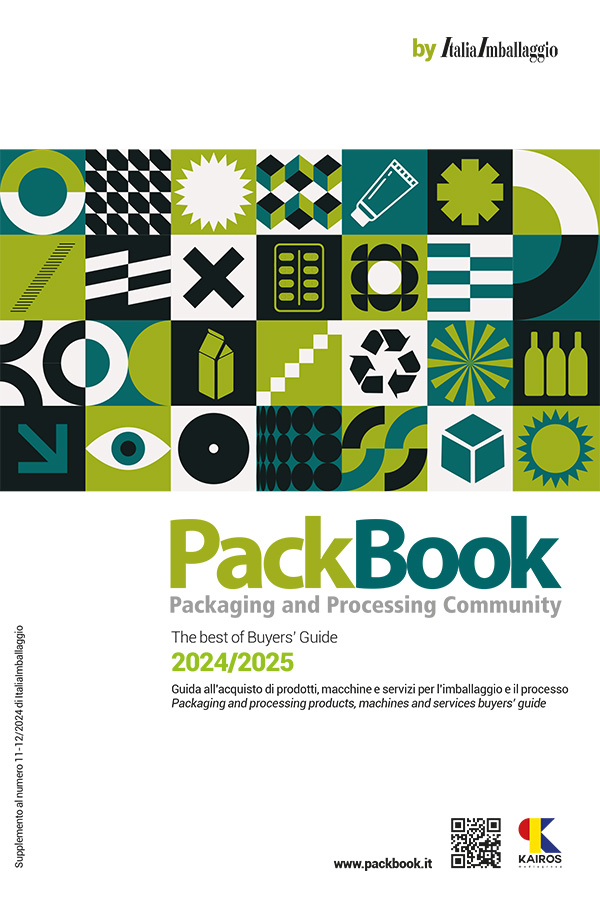